Screen changer for plastric polymer melt filtration
the screen changer consists of the main body of screen changer, slide plate and two breaker plates and electric controlling box, hydraulic station with accumulator.
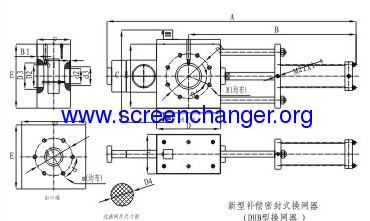
Advantages
patented technology on the sealing system design. Automatic compensation on sealing gap can be realized during screen changing process. Compatible with extruders for various polymers processing at high output.
Filtration screen diameter ranges from 70-360mm.
With highly precise design, the screen has good abrasive resistant, high pressure performance, ensuring large effective filtration area and improving filtration effect. It works well even under high temperature up to 300 ℃ and high pressure up to 50 MPa.
Screen changing time ≤ 2 seconds with pressure accumulator.
Benefits of DHB series of screen changer
leak-free process
Minimum pressure drop
Improved products quality
Reduced waste materials
Reduced downtime & scrap
Reduced inlet pressure at extrusion die
Reduced temperature variations of the melt.
Applications
Blown film and cast film (Bubble pack/ Medical/Food Wrap)
Sheet (Foam/Strapping/Plastic cardboard)
Coating (Hot melt adhesive)
Pipe ( Corrugated/Gas Pipe) and profile
Compounding (Master batch/filler)
Wire and cable extrusion
Tubing (Medical/Industrial/Irrigation)
Fibers ( Monofilament)
Blow molding
Pelletizing (strands and underwater)
Recycling of most polymers