AUTO CONTINUOUS SCREEN CHANGER
AUTOMATIC BELT SCREEN CHANGER
MESH BELT SCREEN CHANGER
AUTOSCREENCHANGER
AUTO CONTINUOUS SCREEN CHANGER
THIS DHW SERIES SCREEN CHANGER IS CONSISTS OF THE MAIN BODY OF SCREEN CHANGER, THE MESH BELT, HEATING AND COOLING SYSTEM. AND THE ELECTRIC CONTROLLING PACK.
How to work
The screen moves across the flow of plastic melt and a fresh screen enters as the spent filter screen exits; removing the impurities from the raw material. The belt screen changer is fitted between the end flange of the extruder and the die. A cassette holding a roll of screen filter is attached to the side of the belt screen changer block. The controlling box of belt screen changer is equipped with a pressure sensor, and a pressure warning device, when the pressure is raise to the preset , it will automatically alarm, at the same time, the screen is replaced automatically. And the cooling system begin to work , the impurity is cooled and moved out with the filter screen.
Red color: heater
Blue color: cooling pipe
Basic Operation
1),Once the auto continuous screen changer has been physically installed. the water lines connected, heaters connected to the controller, and when required the pressure sensor is fitted and connected to the controller, you are ready to follow the simple Start Up.
2),The filter mesh belt enters the main body of the ScreenChanger from the mesh belt box, It passes across the flow channel and then exits the ScreenChanger body carrying with it any contaminates.
3),When the extruder is running, the auto continuous screen changer unique design uses an integrated process relying on cooling and heating of the melt and pressure to control the change of the screen.
Time for screen change
1. Cooling – water (8 –20 degrees C) is circulating in the entrance and exit blocks. This creates a pressure tight Polymer Plug or seal at both the screen Entry port – keeping the polymer in and air out and at the Exit port. At the Screen Exit the water-cooling maintains a sold Polymer Plug (seal) that contains the filter screen.
2. Heating – When a screen change is needed the two cartridge heaters at the exit, heats the tip of the Polymer Plug permitting it to move. Four high quality cartridge heaters maintain temperature levels in the main section of the auto continuous screen changer
3. Screen Advances - The Polymer Plug (containing the screen and impurities) that is under pressure moves out of the exit for a predetermined length determined by the timer or pressure regulator or manual operation. This also moves the contaminated screen across the flow of plastic and a fresh screen section enters.
Widely used for:
1. Extruders (Plastic Extruder, Cast Film, Blown Film Extruder, etc)
2. Plastic pipe production line
3. Pipe, PA, PET and PVC sheet extrusion lines
4. Pelletier, granulation, Non-woven, Plastic recycling and Monofilament machine
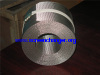